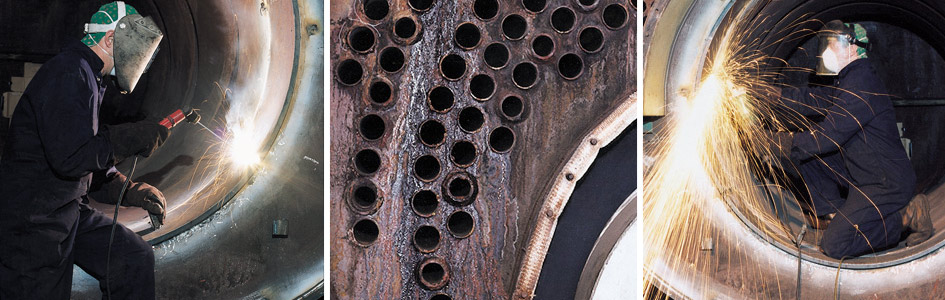
Replacing sections of the outer shell front and rear and part of the furnace tube on this unit involves careful planning and preparation between BTH Boiler Services and the client.
Weld cracking, infused land, inter-bead cavities, or laminated plate inclusions are among the many reasons for boiler failure. Failure in this instance was due to toe cracking on the internal fillet welds, which we find constitutes the most common fault of all.
Measuring and setting out the datums, for perfect re-alignment of the burners when they are placed back in position is crucial, so as not to induce flame impingement in the repaired furnace tub
Tube ends projecting into the combustion chamber are prone to failure, the risk of failure is greatly reduced if the projection is removed and the tube plate is machined with 'J' type weld preparation around each tube end to a depth of 3ml plus tube thickness as detailed in BS 2790.
Combustion chamber tube plate after being thinned and the 'J' preps machined. This tube plate was subjected to a magnetic particle inspection (MPI) as part of the quality assurance procedure used by BTH and by many leading Insurance and Inspecting authorities.
A method used to reduce the thickness of the combustion chamber tube plate, to allow more rapid transmission of heat through the combustion chamber tube plate, alleviating the problem of tube plate and tube ends cracking.
Mirror finish and radius of tube ends ensures less heat on tube ends.
All welding is carried out by fully skilled welders to the highest standards. At BTH Boiler Services Ltd we pride ourselves on the finished product. It is the skill of our welders that enables us to maintain the highest standards. All our welders are coded to the list below:-
Repair, replacing and installing pipe work to a plant and the piping in new and hire boilers is one of our speciality.
It's the rebuilding of burner quarls following SBG1 and 2 examinations.
Commissioning and servicing of Burners
This work is carried out on all types of SAACKE, NU-WAY and HAMWORTHY burners by our experienced engineers.
Our experienced personnel can repair various types of stokers ie;
Babcock Stoker style 6 - 8 - 28 & 28x
International Combustion Stoker
Cochran Latchlink Stoker
Proctor Stoker
And many others
By addition of acid to boiler system to remove scale and water treatments deposits
Boiler cleaning method by means of using acids.
We open up the boiler and clean using rotary descaling machine removing as much scale as possible and vacuuming out debris, remove and refurb valves and rebuild boiler using all new jointing following successful inspection of boiler.
Replacement of plain and stay boiler tubes due to rear end cracking caused by overheating.
Re-tubing and Tube Repairs – No matter what size or shape of your unit BTH have the facilities and the capabilities to ensure a first class job is carried out every time. All types of tubes can be replaced whether it be, a water tube or shell type package boiler tube.
Combustion chamber tube plate after being thinned and the 'J' preps machined. This tube plate was subjected to a magnetic particle inspection (MPI) as part of the quality assurance procedure used by BTH and by many leading Insurance and Inspecting authorities.
A method used to reduce the thickness of the combustion chamber tube plate, to allow more rapid transmission of heat through the combustion chamber tube plate, alleviating the problem of tube plate and tube ends cracking.
Mirror finish and radius of tube ends ensures less heat on tube ends.
Safety valves,
Blowdown valves
Feed check valves
Globe valves
Gauge glass valves
Parallel slide valves
Screw down non-return valves
all these can be packed and re-lapped using all new jointing materials in situ.
Or refurbished in house with certification.
SBG 1 & SBG 2 (5 yearly) Examinations
Our skilled personnel will open up the boiler, remove valves and overhaul, remove cladding and insulation, cleaning all areas as required for SBG1/2 EXAMINATION.
This includes cleaning and removal and exposing various welds to allow ultrasonic testing on a 5 yearly basis.
We can arrange all nondestructive testing as required by your inspection /Insurance authorities. Following approval from the aforementioned we re-assemble quarl, insulation and box up boiler.